Discover What is Porosity in Welding and Its Result on Structural Honesty
Porosity in Welding: Identifying Common Issues and Implementing Best Practices for Prevention
Porosity in welding is a pervasive concern that typically goes undetected until it causes significant issues with the honesty of welds. In this conversation, we will check out the key variables contributing to porosity development, examine its detrimental impacts on weld efficiency, and go over the ideal techniques that can be taken on to lessen porosity event in welding procedures.
Common Reasons For Porosity
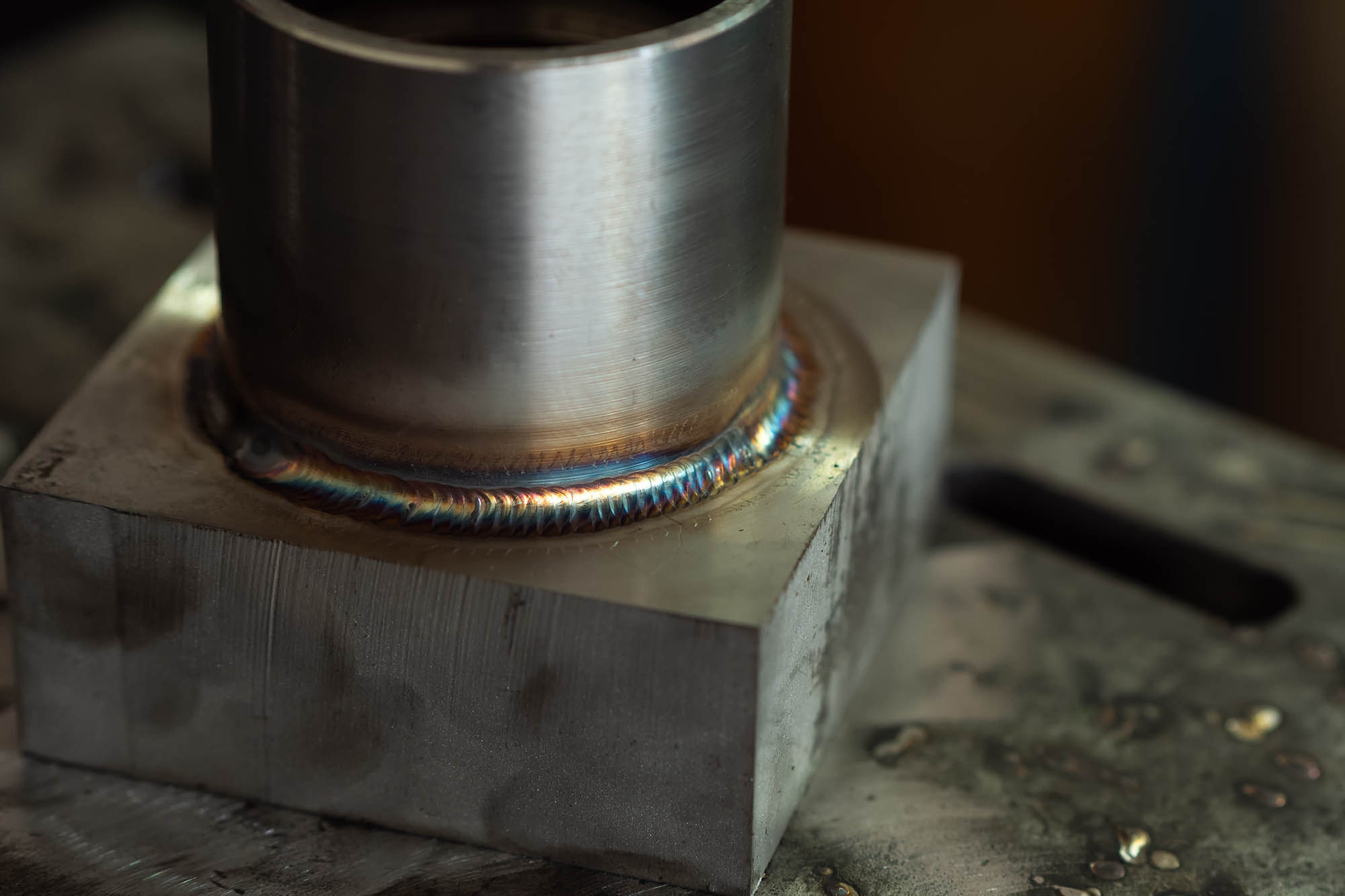
An additional constant culprit behind porosity is the existence of pollutants on the surface of the base steel, such as oil, oil, or corrosion. When these pollutants are not properly removed prior to welding, they can evaporate and end up being trapped in the weld, triggering defects. Additionally, utilizing filthy or damp filler products can introduce impurities right into the weld, adding to porosity issues. To reduce these common root causes of porosity, extensive cleaning of base metals, appropriate protecting gas choice, and adherence to optimal welding specifications are necessary practices in accomplishing premium, porosity-free welds.
Influence of Porosity on Weld High Quality

The visibility of porosity in welding can considerably jeopardize the architectural stability and mechanical residential properties of welded joints. Porosity creates voids within the weld metal, damaging its overall toughness and load-bearing capacity. These voids act as stress concentration points, making the weld a lot more susceptible to fracturing and failure under applied lots. Furthermore, porosity can lower the weld's resistance to rust and other ecological aspects, additionally lessening its longevity and performance.
Welds with high porosity degrees tend to show lower effect toughness and lowered capacity to flaw plastically prior to fracturing. Porosity can hamper the weld's capacity to successfully transfer forces, leading to premature weld failure and potential safety threats in vital frameworks.
Finest Practices for Porosity Avoidance
To enhance the structural stability and top quality of bonded joints, what particular measures can be executed to decrease the event of porosity throughout the welding process? Using the correct welding strategy for the i loved this certain material being welded, such as changing the welding angle and gun position, can even more avoid porosity. Regular examination of welds and instant remediation of any kind of problems identified during the welding procedure are important techniques to protect against porosity and create high-grade welds.
Importance of Proper Welding Methods
Carrying out appropriate welding techniques is vital in making sure the structural honesty and top quality of bonded joints, building upon the structure of reliable porosity prevention measures. Extreme warm can lead to raised porosity due to the entrapment of gases in the weld pool. Furthermore, utilizing the appropriate welding criteria, such as voltage, current, and take a trip rate, is vital for achieving sound Your Domain Name welds with very little porosity.
Furthermore, the option of welding procedure, whether it be MIG, TIG, Full Article or stick welding, need to straighten with the particular requirements of the project to ensure optimal outcomes. Correct cleaning and preparation of the base steel, along with selecting the appropriate filler product, are additionally vital parts of skillful welding techniques. By sticking to these finest techniques, welders can decrease the threat of porosity formation and create top notch, structurally audio welds.

Checking and Quality Assurance Actions
Evaluating procedures are essential to spot and stop porosity in welding, making sure the stamina and durability of the final product. Non-destructive testing methods such as ultrasonic screening, radiographic screening, and aesthetic evaluation are generally used to identify possible problems like porosity.
Post-weld inspections, on the other hand, evaluate the last weld for any kind of flaws, including porosity, and validate that it satisfies defined standards. Executing a comprehensive top quality control plan that consists of comprehensive screening procedures and evaluations is paramount to minimizing porosity problems and guaranteeing the total top quality of bonded joints.
Final Thought
Finally, porosity in welding can be an usual issue that affects the top quality of welds. By identifying the usual reasons for porosity and applying ideal practices for prevention, such as appropriate welding techniques and screening steps, welders can guarantee excellent quality and trustworthy welds. It is necessary to prioritize avoidance methods to decrease the incident of porosity and preserve the stability of welded frameworks.